coel-guides
COEL guide: What to consider when designing a green lab
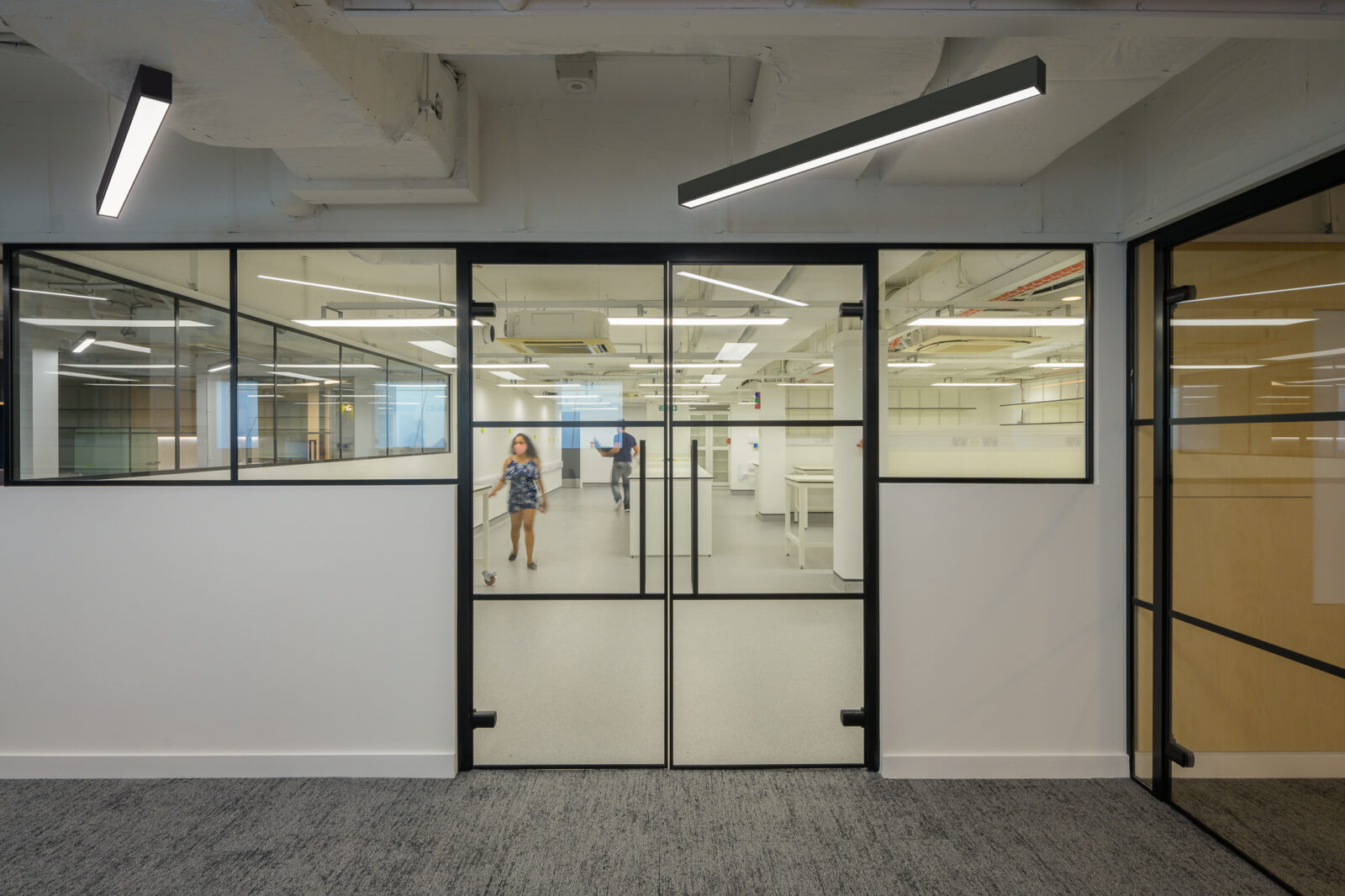
Whilst most of us are switched on to eco-conscious thinking and the mantra of ‘Reduce, Reuse, Recycle,’ for laboratories, achieving green status presents a challenge. Studies show that laboratories consume nearly five times more energy than a typical office space, given their energy-intensive equipment, which often needs to run 24/7.
So, whilst sustainable practices like switching off lights and dialling down temperatures are easy fixes for offices, life science businesses may have cold storage needs, fume cupboards, and heating and cooling requirements, which all contribute to a higher carbon footprint.
So, what can be done?
Thankfully there are a range of small changes – both in sustainable laboratory design and day-to-day practices – which will make a big dent in energy consumption and improve a laboratory’s corporate environmental, social and governance goals (ESG).
COEL’s top tips on how to reduce your laboratory’s carbon footprint
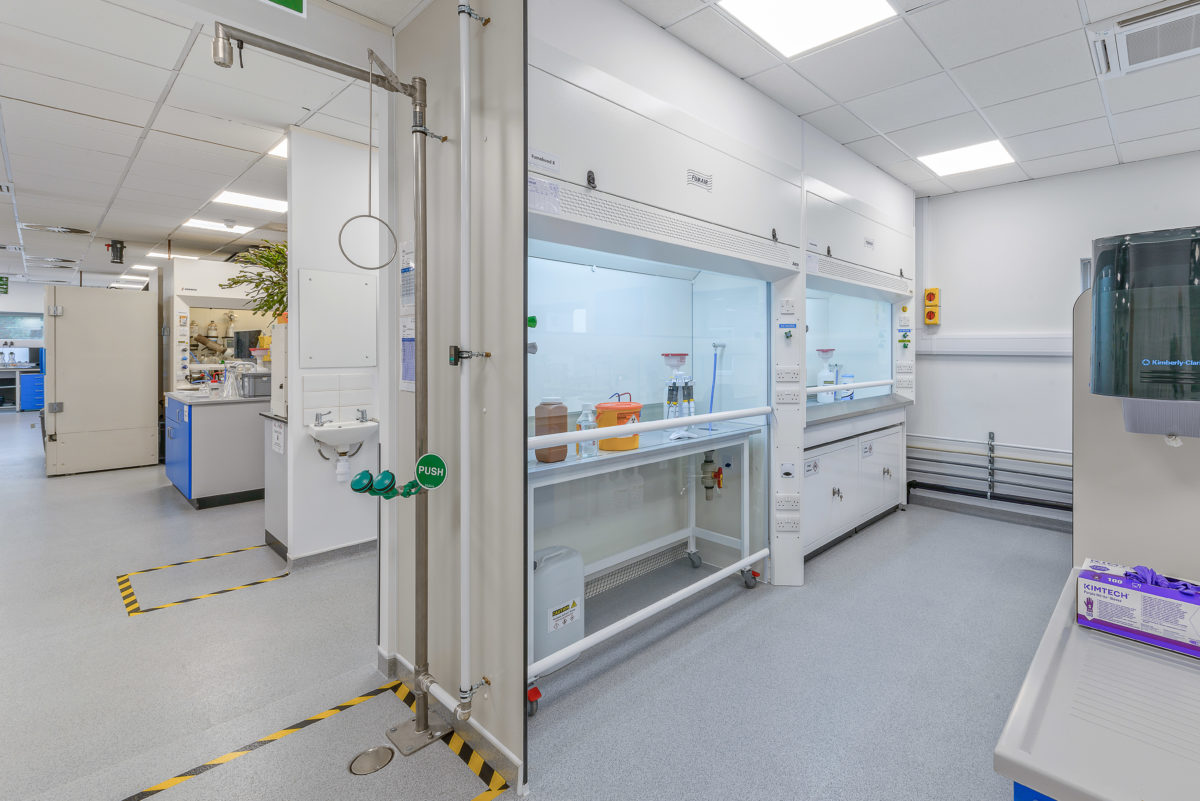
1. Develop a plan
The scientists are the experts, and each laboratory is unique (wet, dry, research?) which is why COEL’s lab designers work closely with key stakeholders to understand the nature of the business, and devise a green plan tailor-made to their requirements.
Here’s some considerations:
a. Include as many stakeholders as possible in your sustainability strategy, from health and safety experts and engineers to lab users and architects, to fully understand how each department can do their bit.
b. If it’s a new build lab, ensure sustainability is prioritised from the outset in design and fittings, with eco goals set for various stages of the build.
c. Each member of the laboratory has a part to play so educate staff on best practice to save energy. This will ensure employees feel invested in creating a green lab which will not only save the business money, but benefit their lives by safeguarding the planet for their family and future generations.
“One of the issues we have experienced in the past is that when companies are looking to build a new facility or looking to refurbish an existing one, they usually go straight for the ‘bells and whistle’ option, often over engineering the space.
“Speaking to the right person and getting the brief down accurately early on is key. I’ve lost count of the time we have spent redesigning projects because the client has over engineered and, in some cases, installed items that they don’t need from day one, which could be fitted later.”
Dean Powell, Group MEP Director
2. Design for your people
Mechanical and electrical experts should be engaged early on to ensure that your laboratory is a safe space for employees working within it. Is the lab well ventilated? Are harmful chemicals stored correctly? What about the wellbeing of staff, who should have a comfortable working environment?
Here’s some ideas:
a. A safe lab needs clean air, so should have an effective HVAC system managing the heating, ventilation and air conditioning. COEL’s mechanical and electrical division have vast experience of fitting a variety of energy-efficient ventilation, extraction and air conditioning systems. Ensure furniture is moved away from the air supply, to maintain good circulation.
b. As HVAC is a big energy cost to laboratories, installing real-time air quality sensors and filtering conditioned air could reduce energy consumption costs, though it may not be possible in labs where air quality changes might affect trial results.
c. Let’s talk fume hoods! One of a lab’s biggest inefficiencies, a fume hood burns the same level of energy as 1,733 gallons of gas every year. Shut fume hoods if not in use because when a sash is left up, it pulls room air into the hood whilst pumping in reconditioned air from outside. Add ‘shut the sash’ stickers to fume hoods to remind staff.
d. As scientists spend long periods of time working intensely in controlled lab spaces with a prescribed level of light and temperature, provide a welcoming contrast to this with relaxing breakout spaces, decorated with calming blues and greens, and decked out with lush plants to boost energy levels and lift moods.
PROJECT FOCUS: WREN THERAPEUTICS
COEL’s design and fit-out of laboratories and office space at Wren Therapeutics championed staff wellbeing. Whilst the labs received a complete overhaul, the adjoining office space was designed as a soft antidote to the clinical areas, with a dramatic dark blue colour palette, stunning suspended biophilic arrangements and uplifting ambient LED lighting.
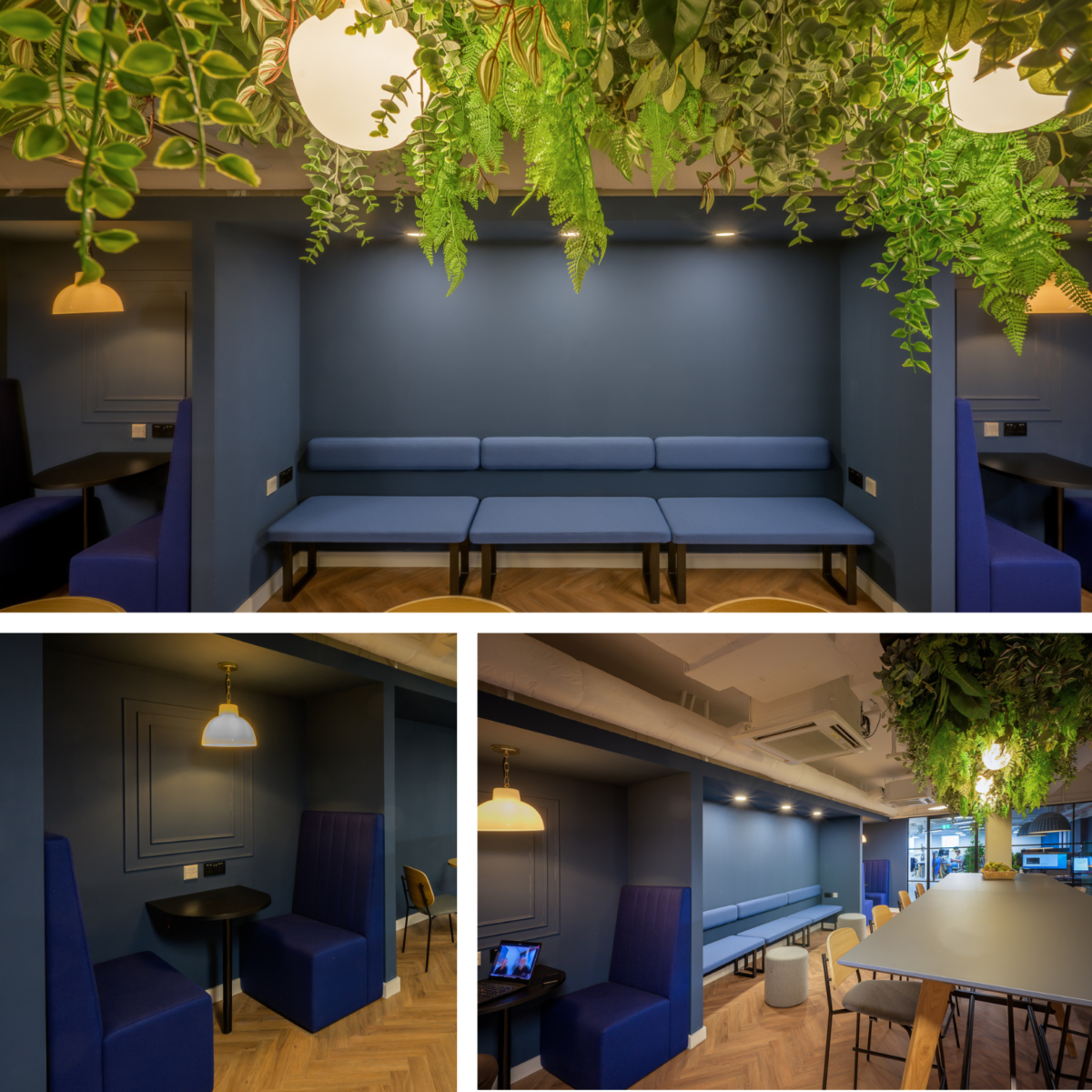
3. Consider the environment
Laboratories should bear in mind their impact on the neighbouring environment, as well as further afield by managing hazardous emissions and disposing of waste responsibly.
Here’s how:
a. If a new laboratory is being built, planners should embrace the principles of ‘conscious design’, ensuring the site is accessible by road, public transport and bike, and does not cause excessive light and noise pollution. Take this one stage further, and incorporate health-related resources such as walking paths, fitness equipment and green spaces to up your ESG rating.
b. Existing laboratories should look at their plastic use. One study suggests that academic research labs produce around 5.5 million tons of plastic waste each year, owing to the popularity of disposables such as plastic pipette tips, gloves, syringes, filters and bottles which end up being sent to landfill. As these may be contaminated with harmful substances, recycling isn’t a viable option. Consider switching from plastic to glassware which can be sterilised after use and re-used.
c. Ensure your laboratory has a clear waste management and recycling plan for staff to adhere to. Label bins clearly so the chemical waste goes in the right place, and consider popping a composting bin in the kitchen for lunch leftovers and paper recycling bins next to printers and photocopiers.
d. Consider utilising ‘Green Chemistry’ as an alternative to hazardous chemical compounds, which are difficult to dispose of. Green Chemistry (sometimes called Sustainable Chemistry) advocates creating chemical products (and processes) that either eliminate or reduce the production of harmful substances which have a negative effect on the environment.
e. Liaise with suppliers to see if they can send products in less packaging, and if that’s not possible, see if more eco-friendly packaging is available. MilliporeSigma has a recycling programme which lets clients return plastic foam coolers and chemical containers, which are repurposed into decking, park benches and speed bumps!
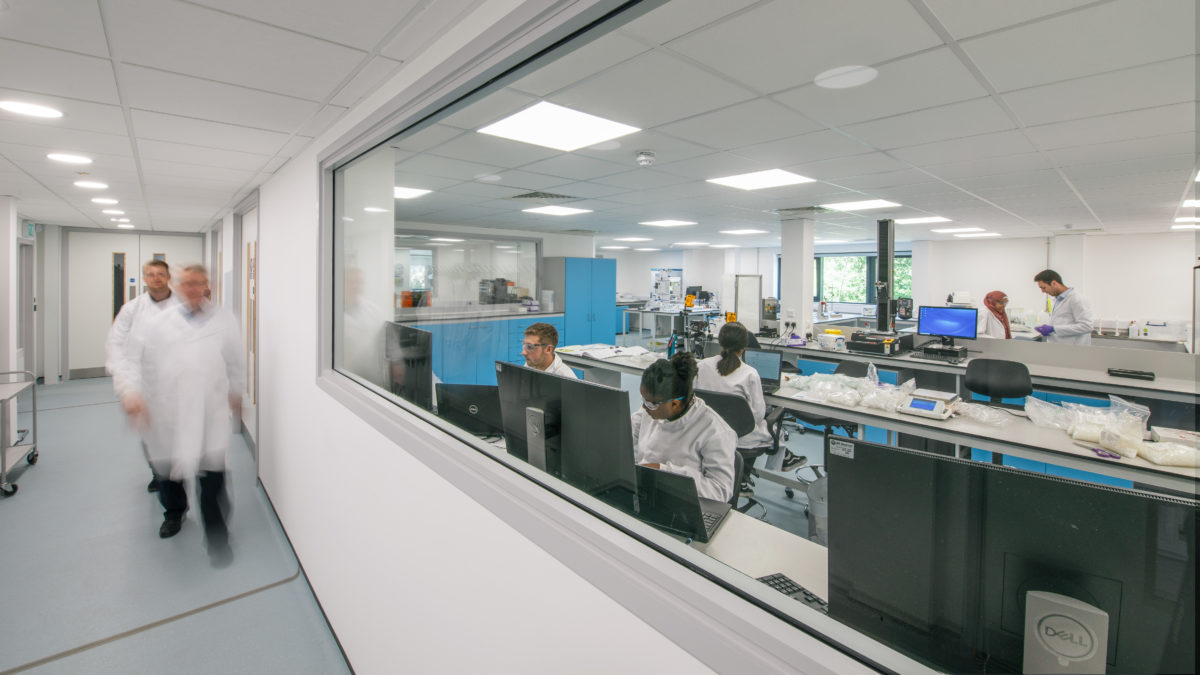
4. Think smart to save energy
Prioritise installing monitoring systems to adapt energy use based on occupancy, and ensure all your equipment, from freezers to water taps, are working efficiently so as not to be a drain on resources.
Here’s some ideas:
a. Smart applications, from lighting to booking systems, can make laboratories far more energy efficient and ensure usage is optimised. So, if staff are booked to work in the lab, leaving the office empty, for example, dial down the office energy supplies accordingly.
b. It seems obvious, we know, but unplug computers and laboratory equipment not in use. Similarly, switch off lighting when not needed.
c. If feasible, adjust ultra-low freezers from -80 degrees Celsius to -70, as this can actually reduce energy consumption by up to 30 per cent and ensure your freezer lasts longer. Defrost -20 freezers once a year to prevent a build-up of ice which may impair performance.
d. Be diligent in cleaning, changing filters and regularly servicing your equipment, to save money and reduce carbon emissions in the long-run. This is especially important for refrigerator door seals and freezer coils, which should be in optimum working order.
e. Turn taps off properly (display a sign to remind staff to do this after each use), as dripping taps cost the UK 2.5 billion litres of water a year. Consider adding low-flow aerators onto taps to reduce water usage.

5. Prioritise sustainable materials
When designing your laboratory, where possible, opt for natural wood fixtures and fittings and sustainable material furnishings to broaden your green commitment.
Here’s how:
a. Choose laboratory furniture made from readily available, renewable or natural materials, such as timber and bamboo, which have the potential to be recycled. If those materials aren’t suitable owing to the type of work your lab specialises in, try to choose a local manufacturer to minimise the environmental impact and carbon emissions.
b. Consider if a piece of laboratory furniture is fit for purpose in terms of lab specifications. So, with work countertops, for example, opt for a robust material able to withstand contact with solvents or corrosives, if these are regularly used in your lab work. Durability is key and means less maintenance, repair and refurbishment.
c. Examine what materials have gone into a piece of furniture and the possible effects they have, especially if potentially hazardous. Designers can review each building material’s Environmental Product Declarations (EPDs) to understand its sustainable attributes.
d. Ensure you dispose of redundant lab furniture in an eco-friendly way so it doesn’t end up clogging up landfill. COEL’s furniture division offers an ethical recycling and furniture disposal service working with innovative business, Sustain.
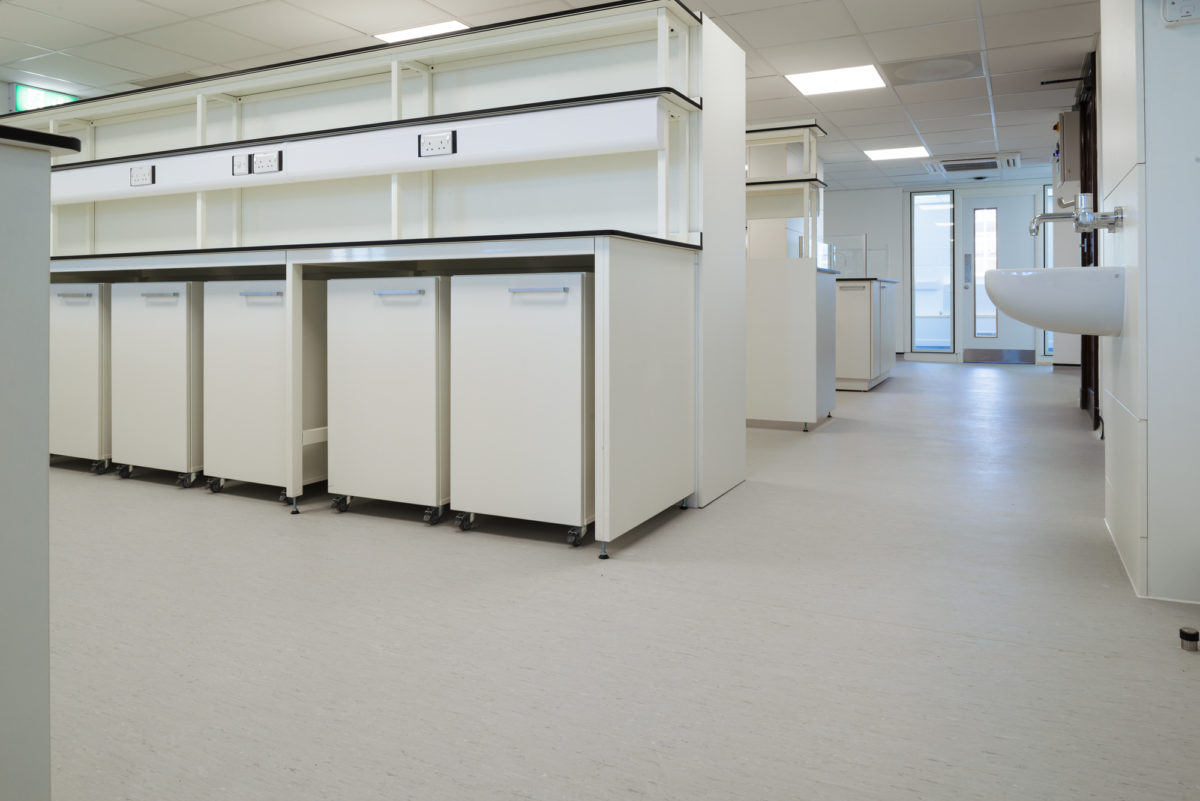
6. Have a future view
If you create a lab which can adapt to your future needs, there will be less demand to replace or refurbish, therefore reducing waste and saving money. Even something as simple as mobile lab storage can make a huge difference.
Here’s how to have the future in mind:
a. The type of work going on within the life sciences world dictates that projects will constantly change as advances are made, so labs should be flexible, to accommodate new staff and regular reconfiguring. Equip your lab with modular flexible units (which can easily be disassembled and reassembled at new facilities), movable workbenches, tables, storages and partitions. This way the laboratory furniture can be re-organised to fit the needs of each new project.
b. Create ‘open space’ research labs to facilitate cooperation between teams and a sharing of resources. Digitise the system so you can book working hours in the shared lab environment.
c. Invest in a digital lab management platform, where all laboratory data and information is available at the click of a button. This means you could essentially go paperless, to save trees, time, space, and reduce work surface clutter.
PROJECT FOCUS: SPHERE FLUIDICS
When repurposing a conference and library space to create state of the art laboratories and offices for Sphere Fluidics, COEL included flexible furniture and storage solutions. Cabinets, draws and work benches were placed on castors to allow for ongoing flexibility in the use of the floor space.
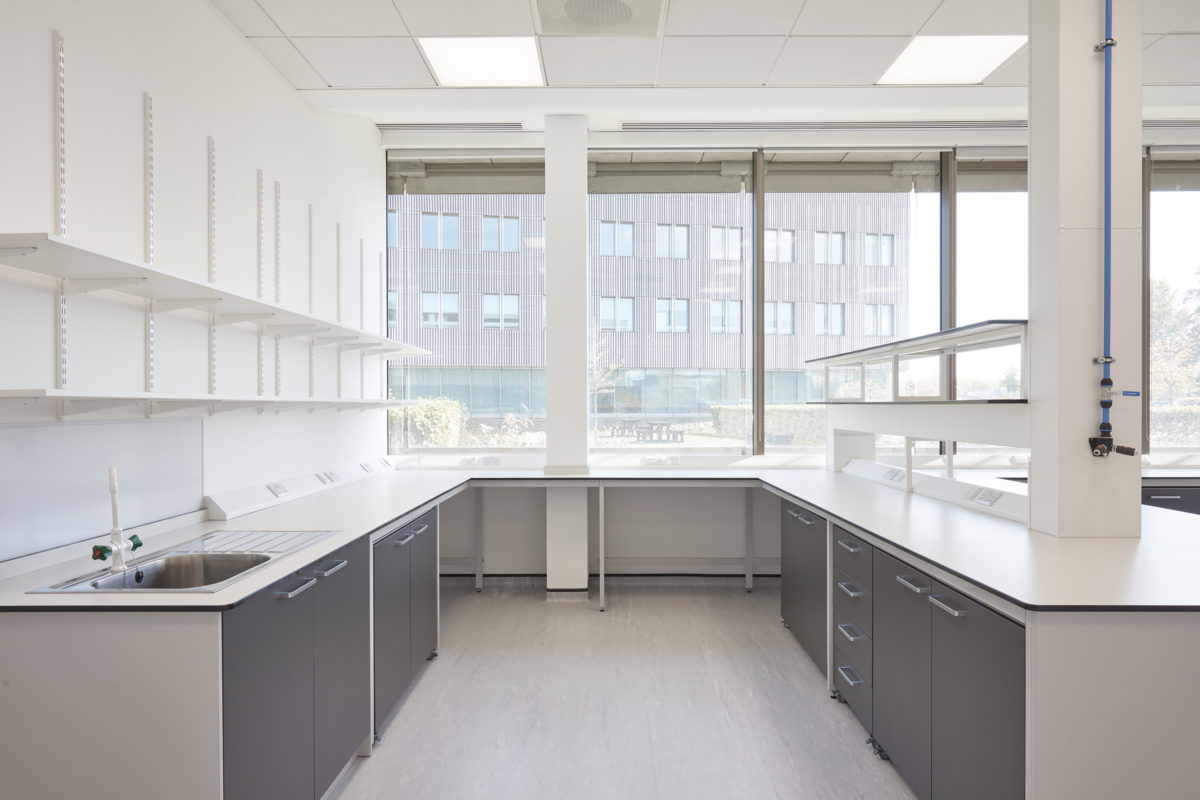
Dean Powell, Group MEP Director concludes:
“By the very nature of the incredible ground-breaking work they do, laboratories are energy-intense workplaces. But by devising an effective green strategy and speaking to the right people early on, there’s much that can be done to reduce energy consumption and create a positive culture of sustainability, which employees can both subscribe to and be proud of.”
If you’d like to work with COEL to make science more sustainable in your laboratory, be sure to get in touch.